Mullins Food Products Empowers Plant Maintenance Technicians with Mobile Access Using Redfig Werks
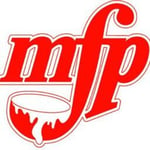
Mullins Food Products (MFP), established in 1934 and headquartered in Broadview, Illinois, is a leading manufacturer and packager of sauces, dressings, and condiments. Operating a state-of-the-art, fully automated facility spanning over 330,000 square feet. MFP supplies custom, private-label products to some of the most respected brands in the food industry.
"We knew we wanted to use SAP® Plant Maintenance, but we wanted to make sure our users had a simple, intuitive interface to work from. Redfig Werks allows our plant staff to efficiently work through their maintenance requests from a mobile device with full integration to our SAP system."
— Joe Sands, IT Director, Mullins Food Products
BUSINESS CHALLENGE:
To ensure optimal plant uptime, MFP relies heavily on SAP Plant Maintenance for preventive and reactive maintenance activities. However, their standard SAP Plant Maintenance module lacked mobile capabilities, necessitating technicians to perform tasks at stationary workstations. This limitation led to inefficiencies, including increased time spent on data entry and delays in accessing critical maintenance information.
SOLUTION:
To address these challenges, MFP implemented Redfig Werks, a BTP-based application designed to extend SAP Plant Maintenance functionalities to mobile devices. This solution enabled MFP's technicians to:
- Execute maintenance orders directly from tablets.
- Submit notifications in real-time.
- Confirm labor time against orders.
- Access and order necessary parts on-the-go.
The user-friendly interface of Redfig Werks facilitated seamless integration with MFP's existing SAP system without requiring additional hardware or significant modifications.
RESULTS:
- Enhanced Efficiency: Technicians reduced time spent on data entry by 40%, allowing more focus on critical maintenance tasks.
- Improved Uptime: Real-time access to maintenance information contributed to a 15% decrease in unplanned downtime.
- Resource Optimization: Streamlined parts ordering and labor time confirmation led to better resource allocation and reduced operational costs.