Leading Confectionery Manufacturer Doubles Warehouse Efficiency by Optimizing Its Existing SAP System
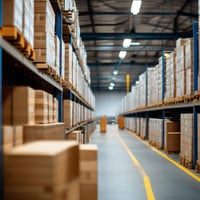
A leading confectionery manufacturer operates a large-scale distribution center in the Chicago area, covering 1 million square feet with 240 dock doors and a throughput of approximately 2,000 pallets per day. The company relies on SAP Warehouse Management (SAP WM) for its logistics and distribution operations.
"The warehouse faced inefficiencies, low visibility, and excessive labor costs. With this solution, we optimized SAP WM with smarter slotting, warehouse segmentation, and automated door assignments. With improved tracking and streamlined operations, we boosted efficiency, reduced costs, and transformed warehouse performance."
BUSINESS CHALLENGE:
The warehouse faced inefficiencies due to:
- Underperforming warehouse efficiency – The facility was only processing 7.6 pallets per man-hour, far below the best-in-class benchmark of 25 pallets per man-hour.
- Lack of visibility into overall warehouse and individual worker performance, making it difficult to optimize operations.
- Inefficient material movement – Forklift operators traveled excessive distances, leading to unnecessary delays and labor costs.
The company was not in a position to implement SAP Extended Warehouse Management (EWM).
SOLUTION:
To address these challenges, the team implemented a structured warehouse optimization strategy within SAP WM, including:
- Warehouse Segmentation – Analyzing product profiles and historical delivery data in order to group products based on how frequently they move and storing related items together.
- Slotting Optimization – Assigning faster-moving items to locations closer to dock doors and at accessible heights.
- Smart Door Assignment – Automating inbound and outbound shipment allocation to reduce unnecessary movement.
- Enhanced KPI Reporting – Introducing new tracking tools to measure warehouse efficiency and labor performance.
RESULTS:
The transformation was completed in just four months and delivered significant improvements:
- 143% increase in picking and putaway efficiency, from 7.6 pallets per man-hour to 18.5 pallets per man-hour.
- 20% overall warehouse efficiency improvement, including non-picking activities like cycle counting and loading.
- 10% reduction in total labor costs.
- The project was executed with near-zero operational impact, requiring minimal training and no downtime during implementation.